浅谈盾构机智能化技术
盾构机智能感知技术
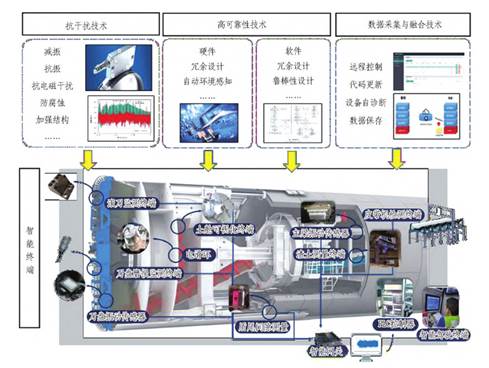
图1 搭载高可靠性智能终端的智能盾构
盾构机智能感知技术是当下盾构机智能化研究的热点,其中最受人们关注的就是超前地质探测技术。在隧道施工中,前方地层假如存在断层、破碎带、岩溶含水体等不良地质体,在施工扰动下可能会诱发突水突泥、塌方等地质灾害,给隧道施工带来严重的生命财产损失。当前用于不良地质超前预报一共有三种方法:激发极化等电法类探测方法、地震波类探测方法、超前钻探法。
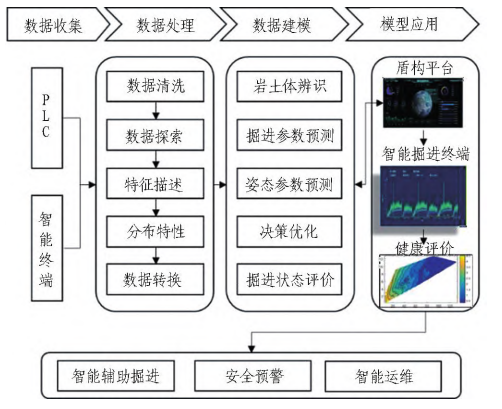
图2 超前预报地质感知系统
盾构机激发极化搭载装置主要包括刀盘电极、护盾电极、边墙电极等部件。在刀盘上安装10-16个测量电极;护盾上安装两圈供电电极8个,每圈各4个,然后沿着边墙布置多圈可移动的供电电极以实现不同测距的测深式观测。进行探测时,盾构机刀盘后退10-20cm,收起撑靴,最大限度减少干扰,刀盘和护盾上安装的电极自动伸出并接触掌子面,主机发送电流并接收信号,探测结束后电极自动回收至刀盘或护盾中,实现了激发极化数据的自动化采集工作。
刀盘刀具检测也是盾构机智能化的一个重要方向,TBM在掘进过程中,通过滚刀在岩面上连续滚压破碎岩体,滚刀刀圈会随着掘进过程不断磨损并偶有弦磨、卷刃等现象发生。据统计滚刀消耗能够占到TBM施工总成本的30%左右,更换滚刀所消耗的时间能占到施工总时长的20%-40%,因此及时识别刀具的工作状态和磨损情况能够有效减少掘进时间、降低施工成本。获取滚刀工作时的转速、磨损等数据,对于研究TBM掘进性能、磨损性能,提高TBM智能化水平有重要意义。
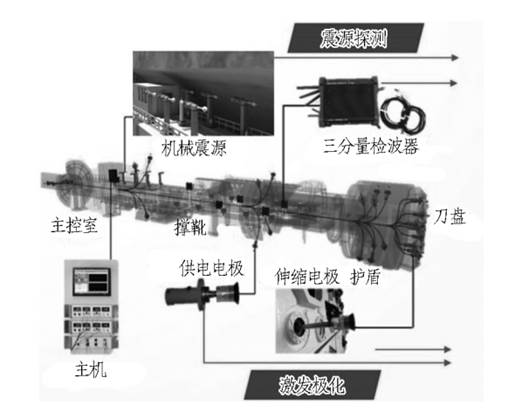
图3 刀具监测,传感器镶嵌在C形块中
基于对工况和现有TBM结构的考虑,选用无损间接测量的传感器是现在TBM刀具磨损检测的主流方式,常选用灵敏度高、有效距离长的自感式电感传感器来测量刀具磨损情况。自感式电感传感器是利用线圈自感或互感的改变来实现测量功能,原理是把被测量的变化转换成自感的变化,通过一定的转换电路转换成电压或电流输出。传感器一般安装在刀盘的外侧,紧邻刀具位置。传感器内部有一个线圈,当电流通过线圈时周围会产生磁场,磁场会受到刀具磨损、位移或其他状态变化的影响,当磁场变化时线圈产生的感应电动势也会变化,将感应电动势的变化经过处理后即可获得刀具的磨损状态。刀具转速检测一般选用高灵敏度的模拟量霍尔传感器,安装在耐磨无磁性传感器保护罩内部,正对刀毂上的永久性磁铁,传感器采集数据经数据传输模块传回上位机,经过软件分析后即可实现对刀具转速的实时监测。

图4 刀盘震动监测
刀盘震动监测通常使用振动传感器(加速度传感器)进行监测,传感器一般安装在刀盘、主梁、鞍架位置。传感器采集的震动数据传输至无线网关,无线网关与主控室工作电脑采用网线连接,通过对震动数据的分析可以得出刀盘的震动状态,操作人员可以根据这些信息及时调整掘进参数,避免高冲击震动对刀盘、刀具的损坏。
盾构机智能决策与控制
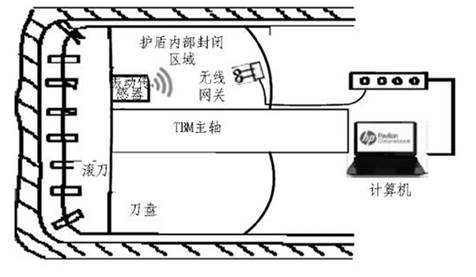
图5 盾构采集数据应用
由于复杂的地层条件导致采集到的掘进参数存在非线性、时变性等特点,因此盾构机智能决策和参数优化的重点在于如何将采集到的数据转化为操作参数。通过开发盾构机智能掘进控制系统,集成岩土信息感知与评价、盾构掘进参数优化、智能纠偏、安全预警等多功能于一体,整体与现有盾构上位机控制系统相结合,实现盾构掘进的决策优化。 针对现有盾构人工经验依赖性较强的问题,利用机器学习或专家系统等方法,与不同地区盾构的大数据库相结合来实现盾构掘进参数的精确预测,从盾构历史掘进数据中“自主学习”以往有经验的盾构主司机操作规则,实现盾构智能控制策略。常用的智能控制策略主要有以下几种:(1)破岩最小比能控制,以节能为最优目标,即以刀盘最小能量消耗来换取最大破岩量。(2)多目标综合优化及驾驶行为,从历史数据的信息挖掘角度出发,分析主司机的操作行为,通过机器学习的方式建立智能控制决策模型,本质是对主司机操作经验的归纳总结和学习。(3)多模态控制MC(Multi-Mode Control)智能控制,可根据控制系统在不同时间和所处的相异状态对控制过程所提出的不同要求,采用自适应的控制策略和相应的控制模式,可以兼顾多种性能指标的要求。
关键工序自动执行机器人
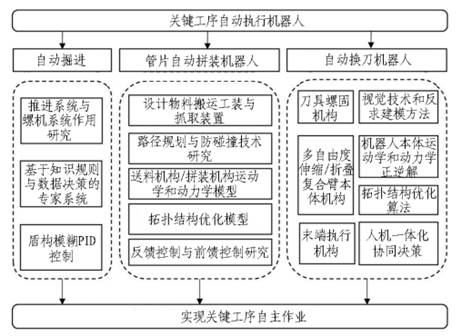
图6 关键工序自动执行机器人
作为智能盾构的执行组件,开发相应的自主作业机器人,是实现盾构自主掘进、管片自动吊运与安装及刀具自动更换等关键工序的重要手段,关键工序自主作业机器人研究路径如图6所示。其中,包含机器人运动学与动力学、路径规划、视觉伺服、机器学习、专家系统、自适应控制、碰撞检测、同步定位与建图 (SLAM)和拓扑结构优化等关键技术。在盾构自主掘进方面,通过深入研究推进系统与螺机等各子系统的耦合关系,使用机器学习、机器人运动学与动力学、专家系统、自适应控制等关键技术,建立以土舱/ 泥水舱压力动态平衡为目标的控制模型,实现盾构位姿调整和自主掘进。在管片自动拼装机器人方面,使用机器人运动学与动力学、路径规划、碰撞检测、SLAM、拓扑结构优化等关键技术,研究装—运—卸—移闭环搬运方法和实施路径,实现管片的安全定位与存放,形成管片自动拼装机构设计与分析方法。在自动换刀机器人方面,基于换刀机器人作业空间狭窄及重载、耐水/压、高定位精度的实际要求,开发多臂复合运动机器人和兼具重载、微调及刀具快速拆装功能的末端执行机构, 使用机器人运动学与动力学、路径规划、视觉伺服、拓扑结构优化等关键技术,重点解决换刀过程中的视觉导航与重载末端精确定位难题,研究复杂工况下电液复合驱动与人机协同控制等技术,实现安全、高效自动换刀。